開発に至った時代背景と技術的背景
真空蒸着技術は、1890年頃、エジソンにより原理が発明されたといわれる。日本では、1956年に初めて連続式真空蒸着装置が導入された。翌年の1957年には、PETフィルムにアルミニウムを蒸着したフィルムベースの金銀糸が発売されている。1960年頃にはアルミ蒸着フィルムが包装用に使われ始め、保香性、防湿性に優れた食品包装材料として注目されるようになった。
透明な無機蒸着については、1964年にデュポン社から「透過性の小さな透明包装用フィルム」という表題の特許が出願され、1969年に特許が成立している。この特許は、例えばポリエチレンのようなフィルム形成性のある有機ポリマーからなる透明でヒートシール性のあるトップコーティング、例えばシリコンオキサイドのような無機の柔軟で透明性のあるガス及び液体のバリアー性のある中間材及び例えばポリエチレンテレフタレートフィルムのような柔軟な透明有機ベースシートからなる、包装材として適した複合フィルム構造体について述べられている。
ここで、シリコンオキサイド膜はバキュームチャンバー内でエレクトロンビーム加熱によりシリコンモノオキサイドを加熱蒸発させることにより付与するとしている。さらに、実施例3ではシリカフラワーを蒸着原料にする例も示されている。また、無機の材質として、ほかにシリコンとアルミのオキサイド、アルミニウムトリオキサイド、ジルコニウムオキサイド、鉛塩化物、銀塩化物等が挙げられている。この特許が食品包装用の透明バリアー無機蒸着技術のもとになっている。
日本ではユニチカで、主としてナイロンフィルムへのケイ素酸化物蒸着の研究が1970年より始められ、1972年には「高度の耐透気性と耐透湿性を有する透明プラスチックフィルム」が出願されている。同社は1973年にはケイ素酸化物を蒸着した透明なナイロン二軸延伸フィルムを「AON」という商品名で販売を開始し、わずかであるがシリカゲル、飴などの防湿包装用に使用された。
珪素酸化物の特性と蒸着成分
蒸着後は、大部分が珪素酸化物の形で蒸着されるものであるから、蒸発物質としては一酸化ケイ素が最も適している。一酸化ケイ素はそれ自身が昇華性であり比較的低温で蒸着できるので、耐熱性の低いフレキシプルプラスチックフィルム上への真空蒸着には特に適している。しかも、蒸着後、特に加熱処理等の後処理を行なわなくても良好な密着性を有している。一酸化ケイ素の代りに二酸化ケイ素を蒸発源として用いることも可能である。二酸化ケイ素は一酸化ケイ素に比べ安価であるけれども、蒸発温度が高いので装置上およびフィルムの耐熱性の面で考慮が必要である。また、ケイ素と二酸化ケイ素の混合物を蒸発源として用いることも可能である。この場合、ケイ素と二酸化ケイ素が高温で反応して一酸化ケイ素として蒸発するものと考えられ、一酸化ケイ素からの蒸着膜と同様の良好な性能が得られる。
ユニチカでは、一酸化ケイ素は蒸発原料として極めて高価なものであるため、ケイ素や二酸化ケイ素のよう安価な蒸発原料を用いて透明でハイバリアー性の蒸着膜を得るために、原料混合比、蒸着条件の検討などを行い、ケイ素と二酸化ケイ素の混合比が1:1.5の場合が最良であること及び混合比が1:2の場合が最もクラックが少なく緻密な膜が形成されることなどを解明した。また、初期の製品は蒸着膜がやや黄色に着色していたため、この問題の解決にも苦労をした。ケイ素酸化物(SiOx)のxの値が小さくなる(酸化ケイ素薄膜の酸化度が低くなる)につれて、光の吸収波長が短波長側から長波長側ヘシフトするために黄色の着色が変化する。これらの問題を解消するために、このxをどの程度の数値に設定すればよいかに苦労した。xは1.5~1.8の間ということになっている。
1976年に本格的な工業化のために、尾池工業がユニチカと共同開発を始めた。シリカと二酸化ケイ素の混合原料を用いてナイロンフィルムへのケイ素酸化物を蒸着する連続生産技術を確立し、1980年から販売を始め、薬品用包装材料に若干使用された。この技術に着目した東洋インキも試験機を購入して研究を開始した。本格的な商業生産は、味の素、東洋インキ及び凸版印刷の共同開発の結果、電子レンジ食品用の包材として、1988年に始まったとされている。東洋インキはその後開発を中断したが、凸版印刷が引き続き生産をしている。その後、PETフィルムについてのケイ素酸化物蒸着の生産技術も確立し、1986年から商業生産が始めている。
物理的方法と化学的方法による蒸着技術
ケイ素酸化物の真空蒸着法には、物理的方法(PVD;Physical Vapor Deposit法)と化学的方法(CVD;Chemical Vapor Deposit法)がある。物理的方法は、10-4から10-6Torr程度の真空中でケイ素酸化物を加熱溶融または昇華させ、そのまま、基材フィルムの上にケイ素酸化物の膜を積層させる方式である。通常厚みは100Åから数千Å程度である。蒸発のための加熱方法は、電気抵抗加熱、誘導加熱、電子ビーム加熱などがあるが、現状の製造装置の主流は、製造装置コストは高いが、製膜速度の高速化がはかれる電子ビーム加熱方式が多い。
化学的方法(CVD)は、有機シラン、有機シロキサン、金属アルコキシドなどの原料をガス状にして真空チャンバー内に導入し、電極ドラムとマグネット間に発生させたプラズマ雰囲気下で化学反応させてフィルム上に特殊なケイ素酸化物を形成させる方法である。蒸着材料に有機シリコンを使用するため、蒸着膜内に有機成分が導入されるので、PVD方式に比べて蒸着膜に柔軟性があり、フィルムが引張られた時のバリアー性の低下が少ないとされている。この方法は大日本印刷㈱で行われている。
ケイ素酸化物の蒸着は、前述のようにフレーク状の一酸化ケイ素やケイ素と二酸化ケイ素の混合物を用いて、電子ビーム加熱法にて成膜している。この成膜中に酸素ガスを導入することで形成されるケイ素酸化物(SiOx)のxの値を制御している。しかしながら、いずれの原料もフレーク状であるため、アルミニウムのようにワイヤー状にして材料を供給することが難しいことと、蒸発速度を上げるために電子ビームの投入電力を高くすると、蒸着材料からの飛沫(スプラッシュ)が発生し、プラスチックフィルムがダメージを受けることがあるため、アルミ蒸着のように蒸着速度を上げることが難しい。また、CVD法も蒸着速度を十分早くすることが難しいとされている。
この問題を解決するために、東洋紡は二元蒸着法を開発し、これを実用化した。PVD法による二酸化ケイ素薄膜は、ガスバリアー性が悪い。これはこの方法ではSi-Oの網目構造が無限ネットワークにはならず、ところどころが未結合の状態となり、その未結合状態(Si-やO-など)はそのまま残存せず、蒸着雰囲気中の水分に起因するH原子で終端される。このため、この方法による二酸化ケイ素薄膜はポーラスな薄膜構造のため、高いガスバリアー性はない。これが上述のケイ素酸化物SiOxのxを1.5~1.8に設定する理由でもあるが、東洋紡では二酸化ケイ素に30wt%以下の酸化アルミニウム(Al2O3)を添加することにより、Si-Oの網目構造の未結合状態の部位を修飾して、より密なネットワークが形成されることを見出し、無機二元蒸着バリアーフィルム「エコシアール」として販売している。二酸化ケイ素と酸化アルミニウムのように蒸気圧曲線が全く異なるため、それぞれの材料を独立した蒸発源から組成比に見合った蒸発速度で蒸発させ、基板となるプラスチックフィルム表面の手前で混合する必要がある。そのため、各々を別々のるつぼに入れて、電子ビームの走査パターンを最適化することで、蒸発した二酸化ケイ素と酸化アルミの蒸気を均一に混合することにより、組成の均一な複合酸化物薄膜を得ている。同社は、この製品は引張試験後のガスバリアー性はアルミ蒸着フィルム、ケイ素酸化物蒸着フィルム、酸化アルミニウム蒸着フィルムのいずれよりも伸展性に優れ、4%程度のフィルム伸張後でも酸素透過度はほとんど変化せず、CVD法で成膜した酸化ケイ素薄膜と同等の柔軟性を有しているとしている。
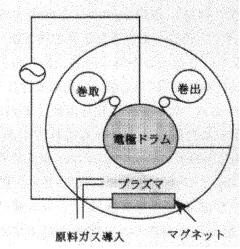